Discover the intricate world of ink manufacturing in our comprehensive guide. Learn about the critical role of industrial mixers, including Ginhong’s top solutions.
Ink is an everyday essential that we often take for granted, whether we’re signing documents, printing important papers, or creating colorful works of art. However, have you ever wondered about the intricate process behind ink manufacturing and how it relies on industrial mixing equipment?
In this comprehensive guide, we will explore the world of ink production, focusing on the critical role of industrial mixers, particularly those by Ginhong, in achieving stable and high-quality ink.
Key Takeaways:
- Ink production involves various components and processes, including mixing equipment.
- Proper mixing is essential to create stable, high-quality ink.
Industrial mixers, like Ginhong mixers, play a crucial role in ink manufacturing. - The choice of mixing equipment impacts ink quality and production efficiency.
What Is Ink?
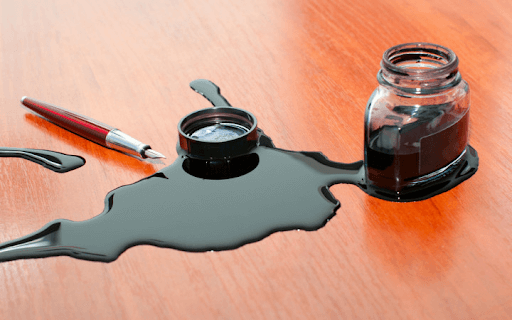
Ink, in its essence, is a liquid or paste that contains pigments or dyes. These components give ink its distinct colors and properties. In the context of ink manufacturing, there are primarily two types of ink: dye-based and pigment-based.
Dye-based inks dissolve colorants in a liquid, similar to adding food coloring to a cake mixture.
On the other hand, pigment-based inks use fine powder suspended in a varnish, forming the base of the ink.
Ink has a rich history, once crafted from natural sources such as fruit and vegetable juices, octopi and squid fluids, and tannins from nuts and tree barks.
How Is Ink Produced Today?
Modern ink manufacturing has evolved significantly from its historical origins. Today, ink is produced through a complex process that involves various components and precise mixing.
The production process must meet several requirements, including the need for stable, homogeneous, and agglomerate-free ink with a sub-micron particle size to prevent clogging of inkjet nozzles. It’s essential to minimize volatile organic compound (VOC) emissions during production.
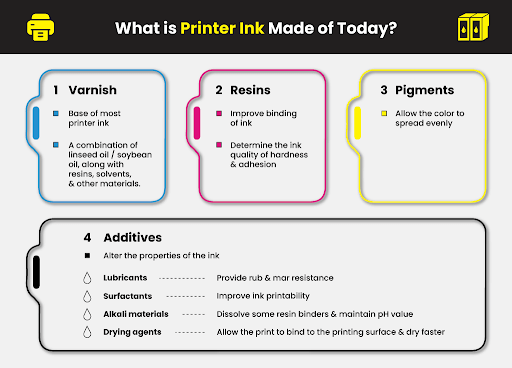
Step 1: Ingredient Selection
- Choose the Ink Type: Decide whether you’re producing dye-based or pigment-based ink, based on the intended use and color properties.
- Select Pigments or Dyes: Carefully choose the colorants (pigments or dyes) to achieve the desired ink color.
- Determine Other Ingredients: Identify any additional components like solvents, surfactants, and binders needed for the specific ink formulation.
Step 2: Preparing the Ingredients
- Pigment/Dye Preparation: If using pigments, finely grind them to a suitable particle size. Dyes are typically in liquid form.
- Mixing Solvents: Combine solvents that are compatible with the chosen pigments or dyes. The solvent mixture should provide the desired viscosity and drying properties.
Step 3: Mixing
- Mix Pigments/Dyes: Introduce the pigments or dyes into the solvent mixture. Ensure thorough dispersion to create a homogenous color.
- Add Other Ingredients: Include any additional components like binders and surfactants, following the specified recipe.
Step 4: Milling
Pass the ink mixture through a milling machine to achieve the desired particle size, ensuring a smooth texture.
Step 5: Filtering
Filter the ink to remove any remaining impurities or particles, ensuring a clean and consistent mixture.
Step 6: Quality Control
Test the ink for color accuracy, viscosity, and other relevant properties. Make adjustments if necessary.
Step 7: Packaging
Fill containers with the manufactured ink, ensuring proper sealing to prevent evaporation or contamination.
Step 8: Labeling and Distribution
- Labeling: Label the ink containers with essential information, including color, type, manufacturer, and safety instructions.
- Distribution: Distribute the ink to various markets or industries as needed.
Note: The specific steps and ingredients can vary based on the type of ink being produced, such as for printing, artwork, or industrial applications.
Important: Industrial Mixing Equipment for Ink Manufacturing
Ink manufacturing heavily relies on industrial mixing equipment, such as Ginhong mixers. These mixers play a critical role in the ink production process by ensuring that the end product meets the necessary quality standards.
Conventional agitators may encounter various problems, including the formation of agglomerates that they cannot break down, leading to long mixing times and the potential buildup of a “scum line” on vessel walls.
Additional equipment, like colloid mills, might be required to achieve the desired particle size.
The Solution:
Processing times in ink manufacturing can be dramatically reduced, and intermediate stages eliminated by using Ginhong mixers. These high-speed mixers are equipped with a powerful rotor that exerts strong suction, drawing both liquid and solids into the workhead. This results in several advantages:
- Dramatically reduced processing times.
- Rapid incorporation and wetting out of powders.
- Elimination of the need for conventional milling.
- The intense shearing action capable of breaking down even hard agglomerates.
- Reduced solvent emissions due to shorter process times.
Ginhong manufactures various machines suitable for ink production, with the selection depending on factors like batch size and ingredient type.
Ink Industrial Mixer Recommendations
For ink manufacturers looking to optimize their production processes, several industrial mixing equipment options are available. Here are some recommended ink mixers by Ginhong:
1. Ginhong Vacuum Emulsifier Homogenizer
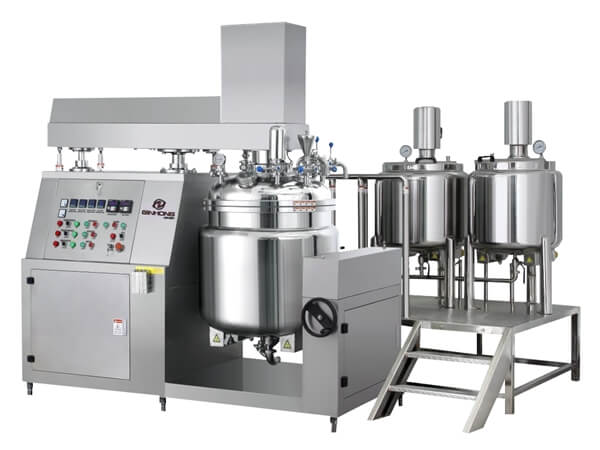
- Elevating the Mixing Process: The Ginhong Vacuum Emulsifier Homogenizer is a game-changer in the ink manufacturing world. It excels at optimizing the mixing process by effectively eliminating unwanted bubbles. When it comes to ink production, achieving a high-quality mixture without agglomerates is paramount. This mixer does precisely that, ensuring that the ink you create is of the finest quality.
- Ideal for Ink Manufacturing: Whether you’re in the business of producing nail varnish or ink, this machine is tailor-made for your needs. Both nail varnish and ink demand exceptional quality, and the Ginhong Vacuum Emulsifier Homogenizer delivers on that front. By removing bubbles and maintaining a consistent mixture, it not only enhances product quality but also provides cost savings for your production process.
2. High Shear In-Line Homogenizer
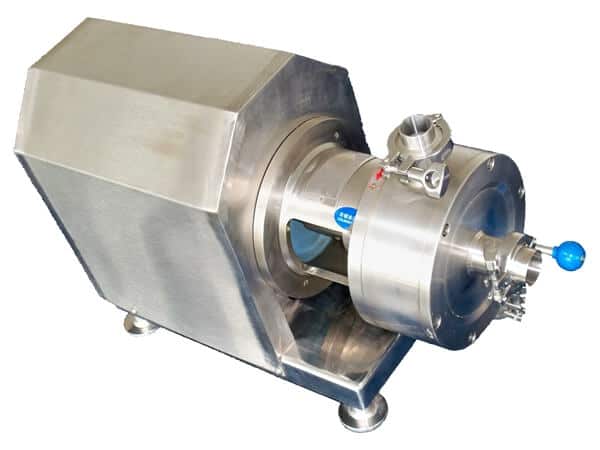
- Continuous Batch Processing: In situations where you’re processing ink in continuous batches, the High Shear In-Line Homogenizer steps up to the plate. It serves as the heart of the RB Vacuum Emulsifier Mixer, ensuring the consistent quality of your ink. Additionally, this equipment acts as a pump for product transport, enhancing the overall efficiency of your production line.
- Space-Efficient Solution: When space is at a premium in your manufacturing facility, this installation becomes a top recommendation. The in-line design not only efficiently processes ingredients but also provides a manifold configuration, catering to multiple ingredient processing. This not only minimizes by-product waste but also promotes reduced batch times and boosts process repeatability.
3. High Shear Batch Mixer
- Tailored for High-Energy Processes: Ink mixing, characterized by high-energy demands, finds an ideal partner in the Ginhong High Shear Batch Mixer. This mixer goes beyond standard mixing; it’s designed to provide a thorough emulsification, dispersion, homogenization, and solubilization of both liquid and solid components. When it comes to the intricate world of ink production, this mixer is a game-changer.
- Precision Engineering: The High Shear Batch Mixer is not just a robust workhorse; it’s also a precision instrument. Equipped with a motor-stator assembly, it ensures that your ink is consistently mixed to the highest standards. For ease of operation, it features a pneumatic lifting system, making it a breeze to handle. Furthermore, it comes with a transmission mount and portable stand, facilitating the entire process.
Advantages of Ginhong Ink Mixer
Ginhong’s range of Ink Manufacturing Mixers are purpose-built for the intricate process of ink production.
Efficient Particle Size Reduction
In the production of ink, achieving the right particle size is crucial. Ginhong’s mixer is engineered to work at high pressure and shear, effectively de-agglomerating solids and reducing particle size. This process ensures that the ink mixture is uniform, preventing clogging and maintaining a consistent texture.
Rapid Homogenization and Emulsification
Our mixer excels in product homogenization and emulsification, critical steps in ink manufacturing. It ensures that pigments and other components are thoroughly integrated into the ink, resulting in a consistent and uniform texture.
Scalable Manufacturing Solutions
Whether you operate on a small or large scale, Ginhong’s mixing machines are up to the task. They can efficiently handle the production of thousands of ink units per day, maximizing your production efficiency and investment returns.
Seamless Pigment and Powder Handling
In ink manufacturing, pigments and powders are frequently used, which can lead to challenges such as clogging. Our industry-grade mixers are equipped to handle these materials seamlessly. With features like a vacuum-filled system, a feeder hopper, and a suction pump, you can effortlessly incorporate powders and liquids, reducing the risk of clogs and downtimes.
Customization for Your Needs
We understand that every ink manufacturing process is unique. That’s why we offer a range of mixer design configurations to choose from, allowing you to select the one that best suits your factory’s requirements and mixing parameters. Additionally, we provide customization options, including automated PLC controls, extra load cells, and additional liquid phase tanks. These features can be tailored to your specific needs, enhancing your ink production process and adaptability.
The Ginhong Ink Manufacturing Mixer offers a comprehensive and efficient solution for the ink industry, ensuring consistent quality and performance in the ink manufacturing process.
FAQ: Ink Manufacturing and Production
How is Printing Ink Made for Various Applications?
Ink is manufactured through a precise process that involves various components and mixing equipment. It plays a crucial role in printing, whether it’s for newspapers, documents, or other materials. The choice of mixing equipment is essential to produce stable and high-quality ink.
What Is Ink Made Out Of?
Ink is typically composed of pigments or dyes, depending on the type of ink. Dye-based inks dissolve colorants in a liquid, while pigment-based inks use fine powder suspended in a varnish. These components give ink its distinct colors and properties.
How Is Ink Produced Today and Where Is Ink Manufactured?
Modern ink manufacturing has evolved significantly from its historical origins. The production process must meet specific requirements, including the need for stable, homogeneous, and agglomerate-free ink with a sub-micron particle size. This is crucial to prevent clogging of inkjet nozzles and minimize volatile organic compound (VOC) emissions. As for the manufacturing locations, ink production facilities are distributed globally.
Why Is Proper Mixing Equipment Essential in Ink Manufacturing?
Proper mixing equipment, such as Ginhong mixers, is vital in the ink production process. Conventional agitators can encounter problems like the formation of agglomerates, leading to long mixing times and the potential buildup of a “scum line” on vessel walls. To address these issues, high-speed mixers like those by Ginhong are equipped with a powerful rotor, ensuring dramatic reductions in processing times and the elimination of conventional milling. This intense shearing action is capable of breaking down even hard agglomerates.