Ointment Making Machine Mixer
Home >> Ointment Making Machine Mixer
WHAT WE OFFER
Ointment Making Machine Mixer
Want to know how ointments are manufactured from the lab to the final, shiny product you see in stores? The manufacturing process takes place mainly in an ointment mixer.
Are You Looking for A Reliable Supplier of Mixers?
Ointment Mixer & Manufacturing Process
The ointment mixer is the cornerstone of pharmaceutical manufacturing. It ensures the creams and ointments we rely on for our health and wellness are safe, effective, and of the highest quality.
Let’s go through the intricate process of ointment mixers and the manufacturing process that brings these essential products to life.
Key Takeaways:
- Precise ingredient selection and formulation are pivotal for the therapeutic efficacy and safety of ointments.
- Advanced mixing equipment, particularly Ginhong mixers, plays a critical role in achieving a homogeneous and stable product.
- Regulatory compliance ensures the safety, efficacy, and quality of ointments throughout the manufacturing process.
- From concept to shelf – the manufacturing stages, from ingredient preparation to quality control, highlight the complexity and precision required in ointment production.
How are Ointments Formulated?
The manufacturing process of ointments starts with the right formulation. This involves selecting ingredients.
Active ingredients are carefully balanced with excipients, stabilizers, and preservatives to create a formula that is effective, safe, and user-friendly.
Below is an overview of the critical components that constitute an ointment formulation
Component | Function | Common Ingredients |
---|---|---|
Active Ingredient | Provides therapeutic effect | Bacitracin, Polymyxin B, Neomycin |
Solvents | Dissolves other substances | Propylene Glycol, Diethylene Glycol |
Emollients | Softens and moisturizes the skin | Lanolin, Petrolatum, Paraffin |
Thickeners | Increases viscosity of the ointment | Waxy/Fatty Alcohol Combinations |
Emulsifiers | Helps mix water and oil phases | Span 83 |
Preservatives | Prevents microbial growth | Parabens, Sodium Benzoate |
Antioxidants | Prevents oxidation and rancidity | Tocopherol (Vitamin E), Butylated Hydroxytoluene (BHT) |
pH Adjusters | Maintains the stability and effectiveness of the ointment | Lactic Acid, Sodium Hydroxide |
Humectants | Retains moisture in the skin | Glycerin, Sorbitol |
Fragrances | Adds scent to the product | Essential Oils, Synthetic Fragrances |
Colorants | Gives color to the product | FD&C Dyes, Natural Pigments |
List of Essential Equipment in Ointment Manufacturing
Here’s a summary of the most important ointment manufacturing equipment:
- Water Phase Vessel: For mixing water-soluble ingredients.
- Wax Phase Vessel: For preparing oil-soluble components.
- Manufacturing Vessel: Where the actual mixing and blending occur.
- Homogenizer: Ensures uniform mixing by reducing particle sizes.
- Storage Vessel: For holding the final product before packaging.
- Transfer and Metering Pumps: For moving the product through the manufacturing process efficiently.
- Colloid Mill: Reduces particle size for smoother consistency.
- Vacuum System: Eliminates air bubbles, ensuring a dense product.
- Heating and Cooling Systems: Controls temperature for optimal mixing and solidification.
Control Panel and Automation Software: Monitors and adjusts manufacturing parameters. - Packaging Line: Prepares the final product for distribution with capping, labeling, and wrapping.
- Cleaning-in-Place (CIP) Systems: Facilitates hygiene with automated equipment cleaning.
Later on, we’ll explore ways to cut down equipment expenses by integrating most of the processes into one or a few pieces of equipment!
Brief Stages of Ointment Manufacturing
- Preparation of Ingredients: Ingredients are categorized into the aqueous phase (water-soluble) and the oil phase (oil-soluble) and prepared in separate vessels.
- Mixing: The core of the process where the prepared ingredients are combined and mixed to form a homogeneous blend.
- Cooling and Filling: The ointment is cooled to the desired temperature before being filled into appropriate containers for storage and distribution.
How Ointment Manufacturing Works: Detailed Manufacturing Process
1. Weighing and Dispensing
The first physical step in the manufacturing process involves weighing and dispensing the raw materials according to the formulation. Accuracy is paramount in this step to ensure the efficacy and safety of the final product.
2. Melting and Mixing of the Base
The process typically starts with the melting of the base, which could include components like waxes, oils, or petroleum jelly. This is done in a heated vessel, often under vacuum to prevent oxidation and degradation of heat-sensitive components.
- Wax Phase Vessel: The wax phase vessel is designed to handle oil-soluble components. It heats and melts the base components such as waxes or oils, allowing for the dissolution of oil-soluble actives and excipients. The controlled heating mechanism ensures that ingredients are melted efficiently without degradation.
3. Preparation of the Water Phase
Simultaneously, the water phase, which might include water, glycerin, or other hydrophilic solvents, is prepared in a separate vessel. This phase may also be heated to dissolve any water-soluble ingredients fully.
- Water Phase Vessel: This equipment is specifically used for preparing the aqueous phase of the ointment. It’s a jacketed tank where water-soluble ingredients are dissolved at controlled temperatures. The water phase vessel is crucial for initiating reactions necessary for the formulation, ensuring that all water-soluble components are fully integrated before they are combined with the oil phase.
4. Mixing of API and Excipients
Once the base and the water phase are ready, active pharmaceutical ingredients and excipients are added. This step might involve the use of a high-shear mixer like the Ginhong mixer, which ensures thorough mixing and dispersion of ingredients, resulting in a homogenous mixture.
5. Homogenization
After the initial blending in the manufacturing vessel, the mixture is passed through a homogenizer. Homogenization is critical for the stability and efficacy of the final ointment, as it facilitates the even distribution of active ingredients throughout the product.
6. Cooling
After homogenization, the mixture is cooled to a temperature where it begins to solidify. Cooling must be controlled to prevent the formation of crystals, which can affect the texture and consistency of the final product.
7. Filling and Sealing
The cooled ointment is then transferred to a filling machine, where it is dispensed into its final packaging, such as tubes, jars, or pots. The containers are then sealed to prevent contamination and ensure the product’s integrity until it reaches the end-user.
8. Quality Control and Packaging
Every batch of ointment undergoes rigorous quality control tests to ensure it meets the established specifications for uniformity, viscosity, pH, and microbial content. Once approved, the products are labeled and packaged for distribution.
Key Considerations in Ointment Manufacturing
- Hygiene and Sterility: Critical to prevent contamination and ensure product safety.
- Yield and Costs: If you use conventional agitators, strained or filtered agglomerates lead to reduced yield output, increased waste, added maintenance, and higher costs.
- Short Mixing Times: If you use conventional mixers, they struggle with hydrating thickeners, extending the mixing process.
- Precision in Ingredient Measurement: You need to ensure consistency and effectiveness of the final product.
Temperature Control: Vital for maintaining ingredient integrity and product quality.
FAQs
- Q: What makes specialized ointment mixers different from other conventional industrial mixers?
- A: Specialized ointment mixers are specifically designed to handle the unique requirements of pharmaceutical products, including maintaining sterility, precise temperature control, and ensuring a homogeneous mix of ingredients with varying viscosities.
- Q: Can ointment manufacturing equipment handle different types of products?
- A: Yes, modern ointment manufacturing equipment is versatile and can be adjusted to produce a wide range of pharmaceutical products, from thick ointments to more fluid lotions, by changing mixing speeds, temperatures, and mixing elements.
Final Words
The ointment mixer and manufacturing process are central to the pharmaceutical industry, ensuring the production of high-quality, effective products. The sophistication of equipment like Ginhong mixers, and strict adherence to regulatory standards all play crucial roles in bringing safe, effective pharmaceutical products to market. By understanding the depth of this process, we gain a greater appreciation for the products that support our health and well-being, backed by the science of pharmaceutical manufacturing.
Industries Served
Vacuum Emulsifier Homogenizer mixers are widely used to make cream, ointment, lotion, and emulsion in cosmetic, pharmaceutical, food and chemical industries.
Request A Free Quote
Have Any Questions?
- +86-517-8689 5589
- info@ginhong.com

Support 24/7
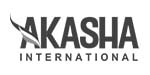
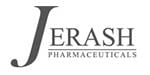
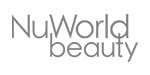
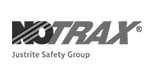
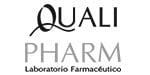