High Shear Mixers
WHAT WE OFFER
High Shear Mixers
Ginhong is one of the leading high shear mixer suppliers in China manufacturing different types of inline and batch mixers, which are widely used to make cream, ointment, lotion, mayonnaise, salad dressing and emulsion in cosmetic, pharmaceutical, food and chemical industries. Follow the product links below to learn more about each Ginhong high shear mixer.
Are You Looking for A Reliable Supplier of Mixers?
Mixer Description
Working with Ginhong as your Mixer Supplier
In almost all manufacturing industries,meeting production demands in a timely manner on a daily basis is key to appease top executive managers.Therefore,when it comes to production,faster is better.But when it comes to meeting product qualities and customer specs,less is more.How manufacturers meet daily demands is well rooted on how efficient the machine is working.Can it perform faster production with less to no downtimes,promote uptimes,and maintain the best product quality?
How well do you know the machine you’re handling?It’s not just how well you know it,but how far your manufacturers go to reach out to you even after sales has been closed,provides you with fast solution,machine education,maintenance and operation.
Ginhong not only engineers and manufactures top of the line Mixer Machines for homogenization mixing,but also knows how to care for suppliers’demands.This is not just about giving the best kind of homogenizer mixer every company needs;it’s also about being the best service provider among others–be it attending urgent needs or unexpected demand.
Is a High Shear Mixer What You Need?All about High Shear Mixers
High Shear Mixers are generally used for mixing products that are not suitable to be mixed at low speed agitation.High Shear Mixers have tip speeds ranging from 10 to 50 m/s and have a very high shear rate ranging from 20,000 to 100,000 s-1.For these specifications,High Shear Mixers are suitable for dispersing solids into liquids,emulsifying immiscible liquids,combining individual products into their proper ratios and dispersion,and breaking down solids and agglomerates.
What is special about Ginhong High Shear Mixers
What sets Ginhong High Shear Mixer apart from other types of agitation mixers is its ability to mill or break down large particle ingredients with a:
- Powerful method–applying high shearing action between materials;
- Refined manner–imparting special physical and mechanical properties and characteristics to the mixed products.
This makes Ginhong High Shear Mixers the best choice for dispersed size reduction and reactive mixing of liquid–liquid emulsification and solid–liquid suspension.Emulsifying liquid to liquid products means dispersing one liquid in a second immiscible liquid,such as mixing oil in water.This is a common processing method for cosmetics,creams,shampoos,sunscreen and ointments.
Intensively Designed,Engineered and Manufactured in a Packaged Deal Fit for Many Industrial Factories
Achieving a homogeneous mix is vital for a high-quality end product,but this is difficult to achieve in practice due to a wide range of factors.For Ginhong,quality is priority and they continue to provide superior quality equipment with the help of their designers and engineers.
Ginhong is very proud to introduce the best equipment performance as a result of intensive Computational Fluid Dynamics(CFD)simulations,and Experimental Fluid Dynamics(EDF).These calculations and experiments were taken into consideration,along with various key design factors such as rotor diameter and rotational speed,distance between the rotor and the stator,mixing time,and the number of generators in the series to reduce power draw,perfect flow pattern precision and maximization of energy dissipation to compete productively in the market.Its mass and heat transfer properties stand as a potential,as it intensifies chemical reaction processes making it more efficient in achieving desired results.
Along with this,their engineers can customize the size and orientation of the mixer with accordance to the client’s requirements suitable to fit in the client’s workshop or factory.
How Ginhong High Shear Mixer works is very simple.An electric motor drives the shaft inside the mixing tank.This shaft is coupled with an impeller which it is rotated at a high speed,driving materials introduced into the mixing tank with strong centrifugal force within it.The components are introduced in the mixing tank at variable speeds,which is essential as some mixing procedure stages don’t require vigorous mixing.
Unlike any typical mixer,the High Shear Mixer incorporates a high fluid shear inside the tank to emulsify or homogenize the material.Fluid undergoes shear when there is a difference in velocity of one area of the fluid to another area.Thus,the materials which are conveyed towards the top of the tank by the force of the revolving lower blades will then be subjected to the powerful shearing force of the upper blades.
Material particle breakup undergoes three essential processes inside the high shear mixer:erosion,rupture then finally,shattering.
In the industry,there are two popular types of High Shear Mixer:1)Batch High Shear Mixer and 2)Inline High Shear Mixer
How Batch High-Shear Mixers Work
In a batch high-shear mixer,the materials are fed from the top of the tank,which contains the mixer being mounted on a rotating shaft at the bottom of the tank.This type of mixer processes materials way faster than the Inline High Shear Mixer type,approximately twice its speed.As such,the Batch High-Shear Mixer is often used by companies with large or bulk volumes of processing materials and where space limitation is not much of a concern.
Designs for this type of mixer may vary:it can be self-cleaning or not.Some designs of the batch high shear mixer can clean by itself during an operating run,while others have to be cleaned manually during scheduled plant preventive maintenance.
How Inline high-shear mixers Work
An Inline High Shear Mixer,on the other hand,is housed with an inlet at one end and an outlet at the other,by which the mixer runs in a continuous operation.The impeller of the mixer acts as a centrifugal pumping device.
Since the Inline High Shear Mixer runs in a continuous manner and is a more compact configuration than the Batch High Shear Mixer,it is more suitable and recommended for manufacturing plants with limited space.The advantages for this type of mixer are the batch times are reduced,promotes lesser by-product wastes and it has a higher process repeatability.
High shear mixing is rapidly and forcefully mixing materials using a high-speed mixer or homogenizer.The intense mechanical forces generated by the mixer break down and disperse particles,resulting in a homogenous mixture.
The cost of a high-shear mixer can vary greatly depending on factors such as size,materials,and features.On average,prices for industrial-grade high-shear mixers can range from around $10,000 to $100,000 or more.Ginhong’s high-shear mixer is of the best quality and is affordable.
A high-shear mixer is used to blend,emulsify,disperse,and homogenize materials in various industries such as food,pharmaceuticals,and chemicals.It applies intense mechanical forces to break down particles and create a uniform mixture or texture.
When choosing among high-shear mixer Manufacturers,consider factors such as product quality,reliability,customer service,and technical support.Ginhong is a top-rated manufacturer in this field,providing high-quality mixers and excellent customer service.
Mixers all comply with Current Good Manufacturing Practice(CGMP)regulations enforced by the FDA.CGMP is vital for quality control of manufacturing plants as it entails proper design,monitoring,and control of manufacturing processes and procedures.
Adherence to the CGMP regulations assures the identity,strength,and quality of manufacturing operations.CGMP also establishes strong quality management systems,robust operating procedures and investigating product quality deviations.
Process Goals
De-aeration
De-aeration reduces product failures by eliminating voids.This is usually common in manufacturing cements or epoxy-based composites when they are subjected to stress.
Deoxidation
Deoxidation is the removal of oxygen from the mixing system to prevent degradation of sensitive ingredients and unwanted chemical reactions during the mixing process.Oxygen can also promote microbial growth which might mix into the ingredients.
Vacuum drying
Moisture and solvent is driven off by the heat produced by vacuum at low pressure.With vacuum we can quickly take the batch material through a series of changes in physical state–from slurry to a paste,and from a paste to a granulation or dry powder.
Solvent recovery
Solvents drawn off with vacuum are easily condensed and captured.This prevents them from contaminating the atmosphere(both inside and outside the plant).The processor can then re-use the solvents or dispose of them to meet environmental requirements.
Solid/liquid injection
Under vacuum,we can inject liquids and lightweight powders into a batch through a sub-surface port in the vessel.This accelerates the mix cycle,especially by wetting out powders instantly.
Densification
A batch that has been agitated and deaerated under vacuum winds up denser than it was initially.This often enables us to mix more efficiently and to ship the product more economically.With densification,the physical properties of the end-product are often improved as well.
Vacuum stripping
A useful tool to lower the temperature of your batch material by evaporation.This is especially helpful when the batch material becomes so thick that it is not in continuous contact with the vessel wall–and no longer transferring heat through the vessel wall to the cooling fluid.
Time Saving
A distinctive feature of the High Shear Mixer relatively is how fast and convenient it is in mixing,emulsifying and homogenizing components as compared to the length of time it takes to get the job done by other conventional high shear mixer.
Fast inherent reaction rates
This property owes to the High Shear Mixer’s ability to intensify and enhance chemical reaction with its high degree of concentrated input energy that produce superior dispersion than traditional mixing methods.
Less Air Entrainment
The overall mixing system forms a close loop,meaning it prevents unwanted air from entering into the system.With less to no air entering the system,cavitation or formation of bubbles in a liquid,which causes blade damage,is prevented.This elongates the life of the High Shear Mixer.
Reduced Waste and Sanitary
The High Shear Mixer’s is equipped with a Scraper made of a Teflon or a non-stick coating.This material is easy to clean,hard to be dissolved in all solvents and can withstand high temperatures.The Scraper gathers material wastes which can be collected without process interruption.
Scalability
Ginhong manufactures a wide variety of mixers with a great range of viscosities and applications.Their extensive range of pumps and process systems are designed to withstand extremities when delivering efficient metering,processing and analyzing.
Pharmaceutical
Almost all pharmaceutical manufacturing processes require preparations of suspensions and handling and processing cohesive powders.
- Assay of Pharmaceutical Products
- Cream&Ointments
- Ophthalmic Solutions
- Vaccines
- Pharmaceutical Syrups
- Sterile Processing
- Tablet Coatings
Food Preparation
Ginhong cares about food safety aside from delivering equipment for quality processing.Some of the most complex Food and beverage processing include blending liquids of different viscosities,dissolving nutrients and sugar,ensuring physical and nutritive properties are met during mixing,process hygiene and making sure overall food rheology specifications are met.
- Meat and Poultry
- Brewing&Distillery
- Cereals
- Confectionery
- Dairy
- Edible Oils
- Flavor Emulsions
- Ingredients
- Meat&Poultry
- Pet foods
Cosmetics and Toiletries
In cosmetic and personal care preparation and processing,challenges are encountered during the mixing process as it is difficult to attain the proper the proper amount of hydration of thickening and suspending agents,maintaining emulsion stability,process hygiene,disintegrating solids,blending liquids of different viscosities and mixing thickeners.It is also an imperative property that cosmetics attain the proper color,fragrance and other physical properties after being mixed.
- Liquid Foundations
- Cream Emulsions and Lotions
- Pigment Dispersion
- Shampoos and Conditioners
- Toothpastes and Dental Whitening
- Creams
- Mouthwash
- Sunscreens
- Moisturizing Body Wash
- Perfumes
- Hair Dyes,Gels and
- Sprays
- Soaps
- Deodorants
- Antiperspirants
- Cosmeceuticals
Chemical Industries
- Asphalt Emulsions
- Fabric Coatings
- Paints and Varnishes
- Mold Release Agents
- Drywall Compound
- Fungicides
- Pesticides and Insecticides
- Solvents and Lubricants
- Toners
- Ink Dispersions
- Printing Colors
- Pigments
- Agrochemicals
- Biofuels
- Drilling Muds
- Lube Oils
- Paints&Pigments
- Paper Coatings
- Polishes
- Rubber Solutions
- Specialty Chemicals </ul
WHAT WE OFFER
Emulsifier Machine Manufacturer
Ginhong is one of the best China-based industrial mixer and blender manufacturers and concentrates on 100% customer satisfaction.
We strive to continually improve on all aspects of our daily operations. What separates us from the competition is not only we manufacture mixers following the highest quality standards, but also we provide every customer with super service.
Ginhong has the experience, knowledge and commitment to both quality and service to solve today’s mixing needs and those of the future.
Industries Served
Vacuum Emulsifier Homogenizer mixers are widely used to make cream, ointment, lotion, and emulsion in cosmetic, pharmaceutical, food and chemical industries.

Equipment for Making Cosmetics
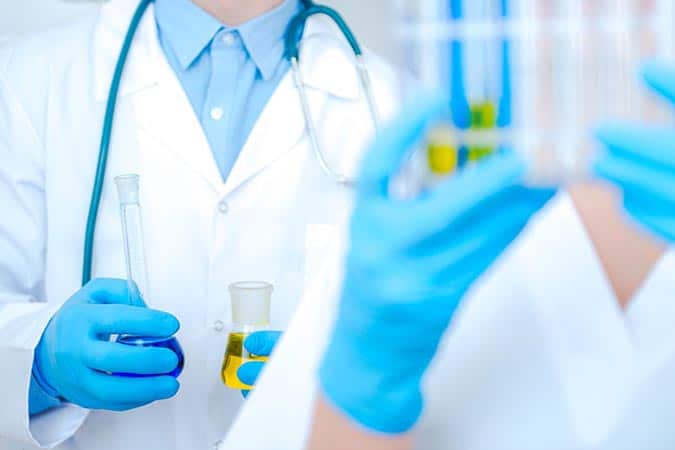
Pharmaceutical Processing
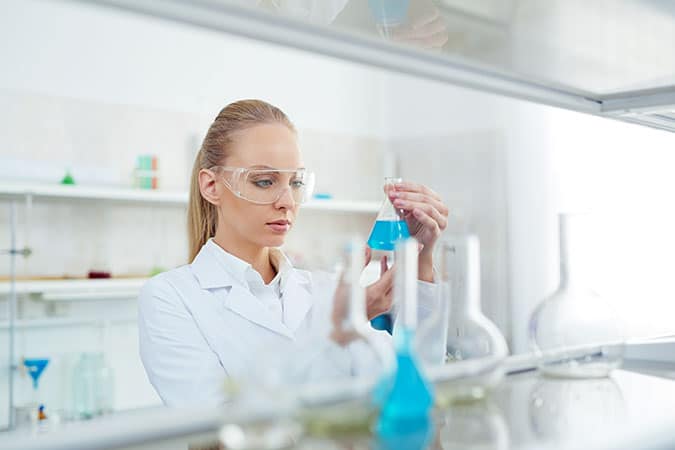
Chemical Processing Equipment
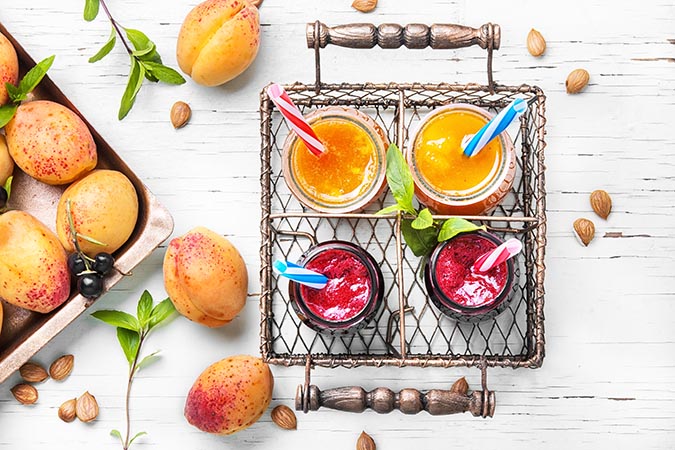
Food Processing Mixers
WRITE TO US
Request A Free Quote
Have Any Questions?
- +86-517-8689 5589
- info@ginhong.com
- +86 18951262589

Support 24/7
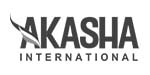
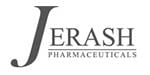
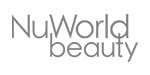
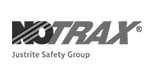
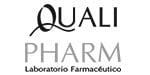